A crane is an important and indispensable device for transporting and lifting goods, especially in pre-engineered steel buildings & steel structures. Learn about different types of factory cranes used by Pebsteel as well as the important factors to keep in mind when designing, selecting and optimizing cranes, thereby helping businesses improve productivity and save costs..
1. What is a factory crane?
A factory crane is a large-capacity crane system, consisting of a crane running on the bridge, combined with one or more crane arms to lift and move materials or goods during the production process.
The structure of a factory crane includes:
- Main beam: The main bearing part, has the shape of box or I-shaped steel. This is the running track of the hoist or trolley.
- Boundary beam: A rectangular box-shaped steel structure with a thickness of 6 to 10mm. This part acts as a shock absorber when the crane moves and touches the end of the track.
- Lifting parts: Hoists or cargo cars, capable of lifting and lowering loads from 1 to 500 tons.
- Control system: The remote control part of the crane or the cabin.
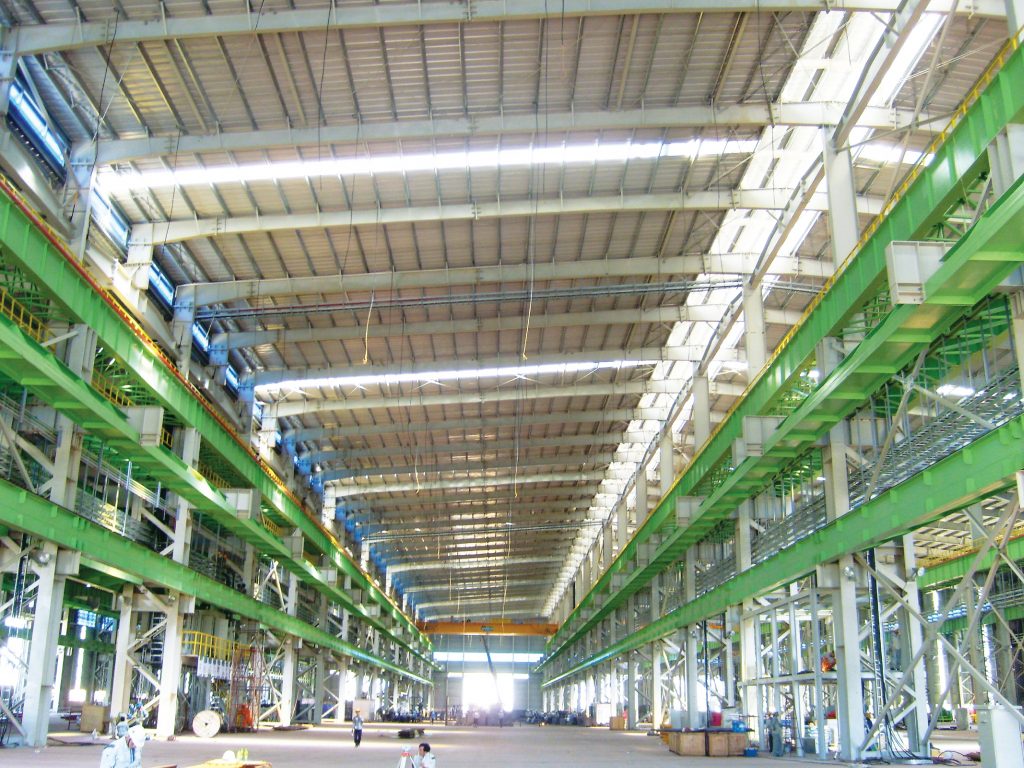
See more: Quotation Of Warehouse Construction Costs Updated
2. Types of cranes commonly used in industrial factories
Nowadays, there are many different types of cranes depending on the shape factor. However, below are the most commonly used types of factory cranes:
2.1. Single Beam Crane
A single beam crane has an independent single beam steel structure with a hoist assembly to lift and lower the goods hanging below. This type of lifting equipment is capable of lifting and lowering medium loads, from 0.5 to 20 tons. With the outstanding advantage of being compact, this type of crane is often used to install small and medium-sized factories. In addition, the single beam overhead crane has a solid structure, ensuring any basic needs.
Some types of single girder crane commonly used in factories are:
- 3-ton single beam crane: A crane with a lifting capacity of 3 tons, commonly used in factories for manufacturing, assembling and repairing machinery and equipment.
- 5-ton single beam crane: A type of crane with a lifting capacity of 5 tons, often used with medium loads in woodworking, steel, cement factories, etc.
See more: Double Layer Steel Floor Structure And Standard Layout Guideline
2.2. Double Beam Crane
A double beam crane is commonly used for businesses and factories with larger loads. The structural design of a double girder overhead crane is generally tougher and stronger than that of single beam crane. This type of crane has a compact and sturdy design, including the following components: 2 main beams, 2 side beams, electrical wiring, control shaft and working platform. At the same time, the double beam overhead crane operation is quite stable, and the crane’s speed can also be adjusted to suit the needs of businesses easily.
Among the types of double beam cranes, the two most commonly used are:
- 5-ton double beam crane:A crane with a lifting capacity of 5 tons, suitable for applications in manufacturing, construction, logistics and other fields that require moving and lifting medium-weight loads.
- 10-ton double beam crane: A crane with a lifting capacity of 10 tons, commonly used in factories and industrial parks with medium to heavy loads.
See more: Pre-engineered Steel Buildings: Components And Applications
2.3 A-shaped Crane
As the name suggests, this factory crane is shaped like the letter A. The A-shaped crane has a variety of sizes and loads up to several thousand tons. Therefore, this type of crane is widely used for transporting, loading and unloading goods with large loads. Moreover, an A-shaped crane is easy to control by hand or by press control.
2.4 Monorail Crane
Monorail crane is a crane with a single rail for moving goods. Monorail cranes are often used in workshops with narrow spaces or hidden corners. This type of crane has the ability to move flexibly in different directions.
This type of crane is commonly used in applications such as manufacturing, assembly and maintenance. It is suitable for moving and lifting light and medium weight goods in a limited range. However, due to the absence of a longitudinal rail system, the Monorail factory crane has a load limit and is not suitable for transporting heavy or large goods.
See more: Bearing Structures and the information that you need to
2.5 Rotary Crane
A type of crane capable of rotating around a fixed point, usually a steel or concrete pole. The rotary crane is composed of a hanging arm and a hoist for lifting and lowering goods. The hanging arm can be rotated from 90 to 360 degrees, depending on the design and use requirements.
The rotary crane is capable of lifting and lowering small loads, from 0.5 to 10 tons. This type of crane has the advantage of saving space, being flexible and able to move goods in different directions. Rotary cranes are often used in factories that manufacture, assemble, and repair machines and equipment.
3. The process of safe installation of cranes in industrial factories
For safe and efficient installation of workshop cranes, you need to follow these steps:
- Step 1: Install 2 boundary beams in 2 main beam head positions. The boundary beam acts as a shock absorber when the crane moves and touches the stop at the end of the track. The 2 side beams need to be attached to the 2 main beams end positions using bolts, screws and connecting accessories.
- Step 2: Install the other remaining parts. The rest of the sets include subfloor, unloading bar, handrail. These units also need to be installed to the main beam using bolts, screws and connection fittings.
- Step 3: Use 2 cranes with a load equivalent to the load of the crane on the track. You need to pay attention to the alignment and balance of the crane when lifting and moving loads to avoid distortion or damage to the equipment.
- Step 4: Crane the crane chamber into the installation position. The crane room is the place where the controller and the cabin are located for workers to control the crane remotely or from within the cabin. The crane chamber needs to be hoisted into the installation position using steel cables and hangers.
- Step 5: Crane and install the hoist to the beam. Hoist is a lifting equipment capable of lifting and lowering loads from 1 to 500 tons. The hoist needs to be hoisted and installed to the beam by steel cables and hangers. Enterprises also need to connect the hoist to the electrical and control systems of the crane chamber.
- Step 6: Install crane cable system and lifting system. Crane power cable system is a power supply system for cranes and related equipment. The lifting system is a system consisting of steel cables, pulleys, gears, motors, etc. to lift and lower goods.
- Step 7: Install the power lines from the source to the electrical cabinet and control room using chicken intestines, wires and connection accessories. Additional attention should also be paid to protecting the electrical conductors from shock, moisture or fire.
- Step 8: Check after completing the installation. Businesses need to perform the following checks to ensure the safety and effectiveness of their equipment:
- Check the connection of bolts, screws and connection accessories of the workshop crane components.
- Check the electrical system, electrical cables, electrical cabinets and control room of the crane.
- Check the operation of the hoist, the trolley, the control unit and the cab of the crane.
- Check the operation of the lifting system, steel cable, pulley, gear, motor, … of the crane.
- Check the operation of the damping system, insurance shield, handrail, etc. of the crane.
4. Crane systems in Pebsteel projects
Pebsteel is one of the leaders in the field of design and construction of prefabricated steel buildings. The Pebsteel construction site crane system is designed to meet the specific requirements of the steel industry.
Below is information about the necessary costs when equipping a crane system in a pre-engineered steel building from Pebsteel:
(1) Reinforce and increase the load force for the main frame system
(2) Provide bridge girders and brackets
(3) Supply and install crane rail
(4) Supply, install and operate the crane system
During this process, Pebsteel is responsible for the execution of items (1) and (2). The remaining items will be assigned to another specialized unit. Here are some typical cranes Pebsteel works with our manufacturers:
- Prefabricated steel warehouse in Binh Duong: has 2 double girders 10 tons, lifting height 9m, aperture 18m.
- Packaging production warehouse in Dong Nai: has 2 single girder shafts of 5 tons, lifting height 6m, aperture 15m.
- Electronic component manufacturing warehouse in Hai Phong: has 4 single beams of 3 tons, lifting height 6m, aperture 12m.
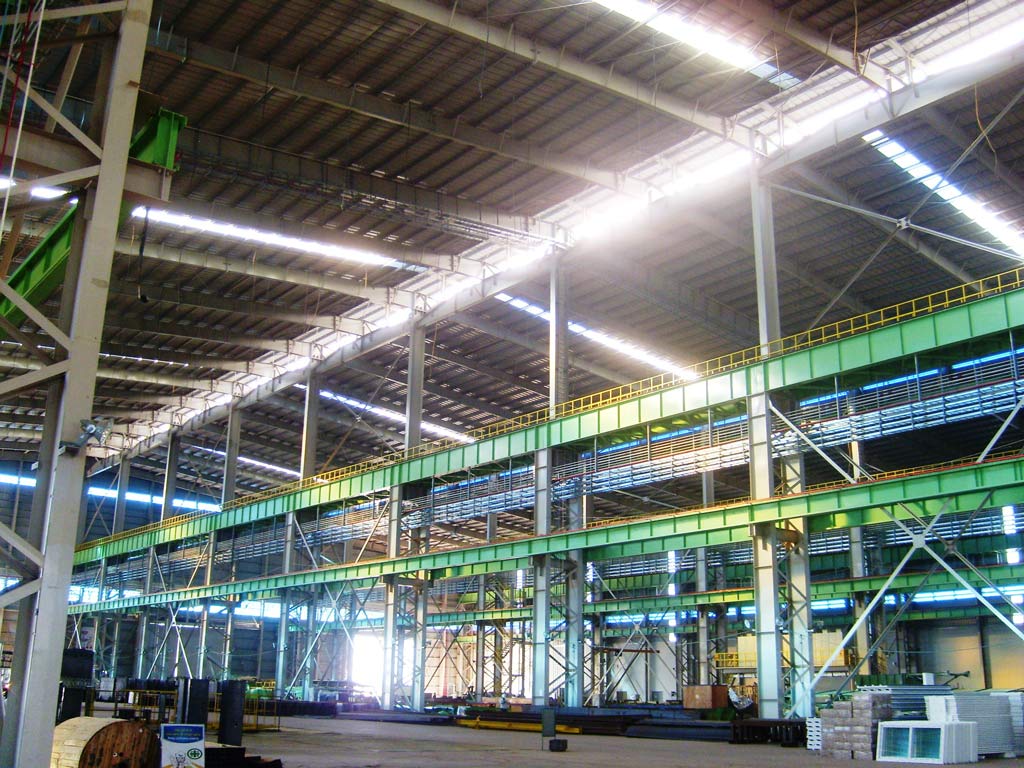
5. Conclusion
Factory crane installation is an important and complicated job, requiring professionalism and a high level of technique. You need to follow safe factory crane installation steps to ensure the efficiency and safety of the equipment. If businesses want to build a pre-engineered steel factory with any of these cranes, please contact Pebsteel via email at Marketing@pebsteel.com.vn or phone number +84 908 883531 for detailed advice.