Today, the demand for construction industrial factories is gradually becoming more common. However, many businesses still do not fully understand the entire process to effectively supervising and manage the of construction contractors. Let’s explore the details of the construction process of an industrial factory in the following article with Pebsteel.
Read more: Warehouse Construction Costs Update 2024
1. Details of the standard industrial factory construction process
The standards for constructing industrial factories are crucial for businesses to assess the quality of the building. The basic criteria in the factory construction process include:
1.1. Construction of foundation anchor bolts
The first step in constructing an industrial factory is the installation of anchor bolts. This step plays a crucial role as it lays the foundation for the entire structure. Any errors during this stage can have a significant impact on the structural components such as beams and columns.
The anchor bolts must be securely welded to the steel reinforcement of the foundation. Welding the anchor bolts should take place after the installation of the formwork and steel reinforcement of the foundation has been completed, ensuring the stability of the formwork. Additionally, it is essential to cap thebolts carefully to prevent the rustiness or dirt buildup on the threaded ends.
1.2. Transportation of the materials and components
The raw materials and steel components, after being fabricated and quality-checked, will be transported to the construction site. Once fully gathered at the designated location, the construction team will begin the erection of the factory structural steel frame according to the technical drawings.
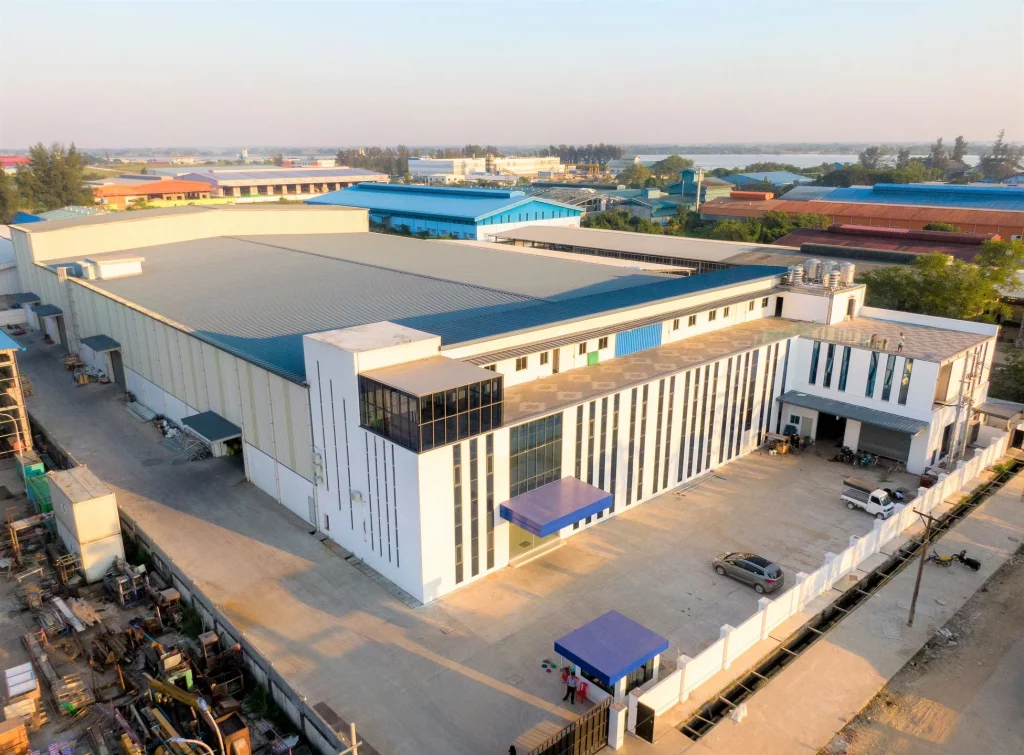
Read more: Standard Factory Construction Process
1.3. Erection of the columns, trusses and purlins
At this stage, due to the heavy weight of the steel components, machinery support is required for lifting and transportation during installation. Below are the specific construction steps:
- Install the rigid bracing.
- Assemble the beams and rafters.
- Complete the bracing system.
- Install the roof truss and purlins.
- Install the gable end truss.
- Assemble the purlins and girts.
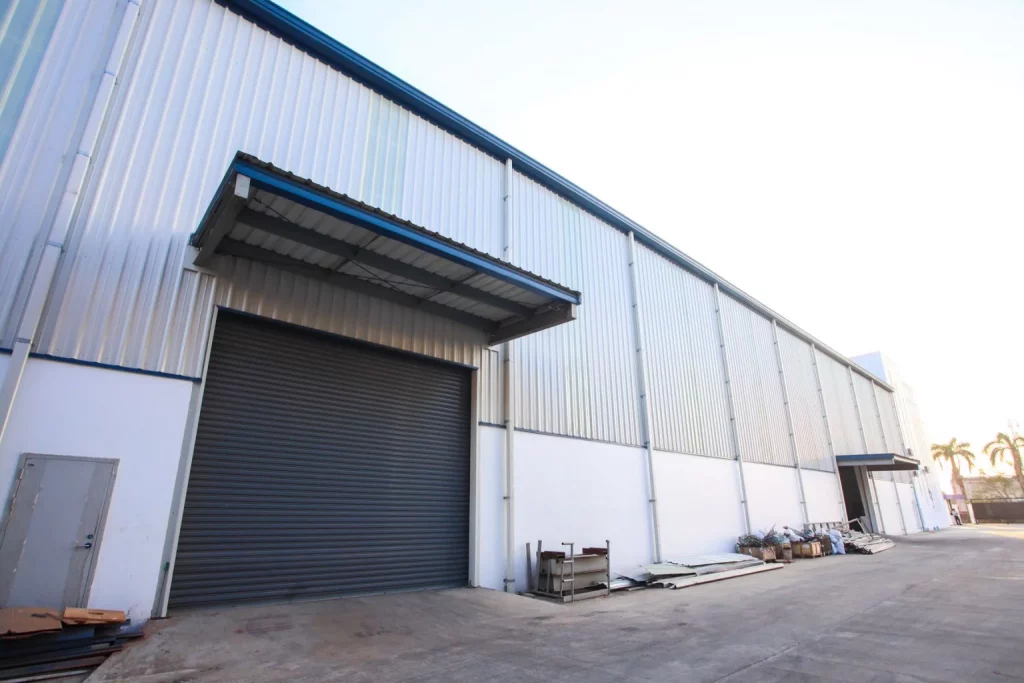
Read more: What is a Steel structure? Main type of steel structure building!
1.4. Erection of the prefabricated concrete floor slabs and walls
Installing the concrete floor and wall for the industrial factory should be carried out following the technical design specifications. Based on the predetermined anchor bolt positions, concrete panels are lifted and installed precisely. After ensuring proper alignment with the roof truss/upper bracing system through bolt connections, construction workers will securely tighten the bolts both above and below to maintain a fixed position.
1.5. Installation of the roof sheeting for factory
The process involves placing each sheet of metal onto the rails and securing them with iron hooks. Then, the rails are pulled to lift the metal sheets onto the roof of the industrial factory. Construction workers will attach these metal sheets to their designated positions on the roof purlins. This process continues until the roof section is completed.
1.6. Constructon of the infrastructure and technical systems of the factory
The infrastructure of an industrial factory includes elements such as the transportation network, drainage pipe system, ventilation, gutters, wall sheeting materials, etc. The technical system includes fire protection, communication, electricity, water, and so on. Additionally, there is the ability to construct additional infrastructure amenities such as plasterboard ceilings, green gardens, etc., to enhance the aesthetic aspect of the project.
1.7. Acceptance, handing over and putting the project into use
Once the above steps are completed, the contractor needs to inspect the quality of the columns, rafters, bolts, and roof gable and eave trims, as well as any openings for louvers. Afterward, the entire factory will be cleaned and tidied up. If everything meets the requirements, the contractor will proceed with the final inspection and hand over the industrial factory to the client.
1.8. Industrial factory warranty
After handing over the factory, if any problems occur during operation, the construction contractor will do the warranty for the. Each contractor will have a different warranty policy.

2. Some notes in the process of building industrial factories
- The most crucial part of constructing an industrial factory is the foundation structure, so the construction contractor need to pay special attention to this phase.
- Careful and precise calculations of the columns and steel rafters length is essential to avoid excess or insufficient steel allocation.
- To ensure the stability of the frame structure, the installation of bracing for the factory should be carried out securely. During the construction process,installation of the rigid bracing should be focused from the beginning,, followed by the installation of other elements such as columns, rafters, purlins, and roof bracing.
- The contractor needs to choose the size (height, thickness) and function of precast concrete panels that are suitable for the intended use.
- The installation of metal roof sheetings must adhere to standards, ensuring that their connections are aligned and form right angles with the purlins to guarantee the quality and aesthetics of the project.
- The safety of the workers during construction should always be ensured by providing them with adequate protective equipment and avoiding construction during unfavorable weather conditions.
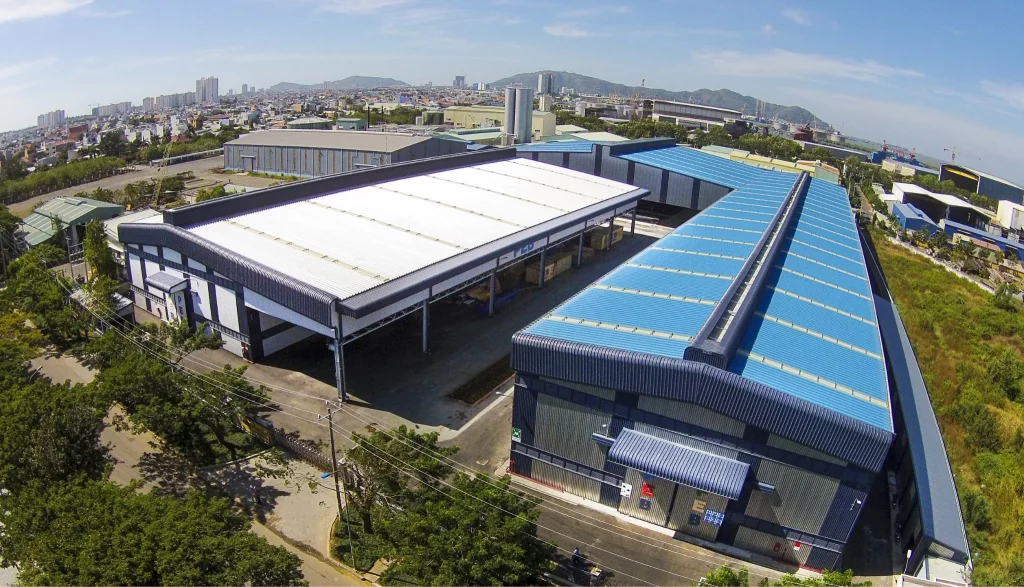
3. Detailed steps for constructing industrial factories according to standards
3.1. Planning and Design Preparation Phase
Identifying the Needs and Purpose of Factory Construction
- Analyze the production scale, type of product, and technological process to determine the specific area, structure, and technical requirements for the factory.
- Choose a suitable construction site that is convenient for transportation, raw materials, and labor supply.
- Consult experts in construction and manufacturing to make optimal decisions.
Creating a Detailed Plan for the Factory Construction Project
- Prepare detailed design drawings of the factory, including the floor plan, 3D perspective, etc., clearly showing dimensions, structure, materials, and other technical details.
- Estimate the project cost, including material costs, labor, machinery, transportation, and other expenses.
- Develop a specific construction schedule, dividing it into phases and setting completion times for each phase.
Industrial Factories Land Plotting
- Proper layout is crucial in the construction steps of a factory. A well-thought-out, optimized layout is a key factor in the overall quality of the plant and production area.
- Rational layout of factory areas not only facilitates easy movement for workers but also makes product transportation significantly more convenient. Additionally, a good layout helps save space and maximize the use of the factory.
- Companies typically allocate space according to the function of each area, such as production areas, production support areas, front industrial areas, storage, and transportation zones.
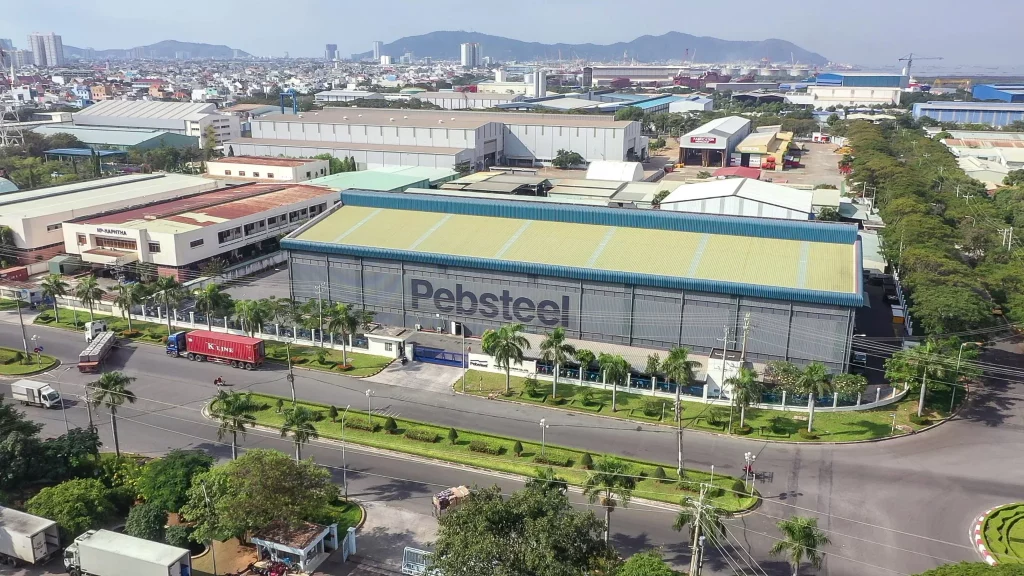
Preparation of Construction Site
- Define the boundaries of the construction area and proceed with leveling the ground, ensuring it is flat, clean, and at an appropriate height.
- Clear obstacles, waste, and unnecessary materials from the construction site.
- Ensure a good drainage system to prevent flooding during construction.
- Maintain safety corridors for the movement of vehicles and construction equipment.
Anticipating Future Factory Expansion
- When planning an industrial plant, businesses should foresee future possibilities, especially the potential for production expansion.
- When selecting a construction site, consider whether the surrounding area can be purchased or leased for future production. The layout should also be considered, as the area might later be used for additional factory buildings, auxiliary structures, or warehouses.
- Building a factory and creating layout processes require coordination among parties during construction.
Preparing Construction Materials and Workforce
- Order factory construction materials according to the quantities and types specified in the cost estimate.
- Check material quality before use, ensuring it meets technical requirements.
- Hire skilled labor with expertise and ensure safety during construction.
- Prepare necessary construction equipment such as cranes, excavators, concrete mixers, steel cutters, etc.
Selecting a Reputable Contractor
- Research reputable industrial factory construction contractors in the market.
- Compare the capabilities, experience, prices, and accompanying services of different contractors.
- Consult previous customers of contractors to evaluate construction quality.
- Choose a reputable contractor who ensures construction quality, progress, and post-construction warranty.
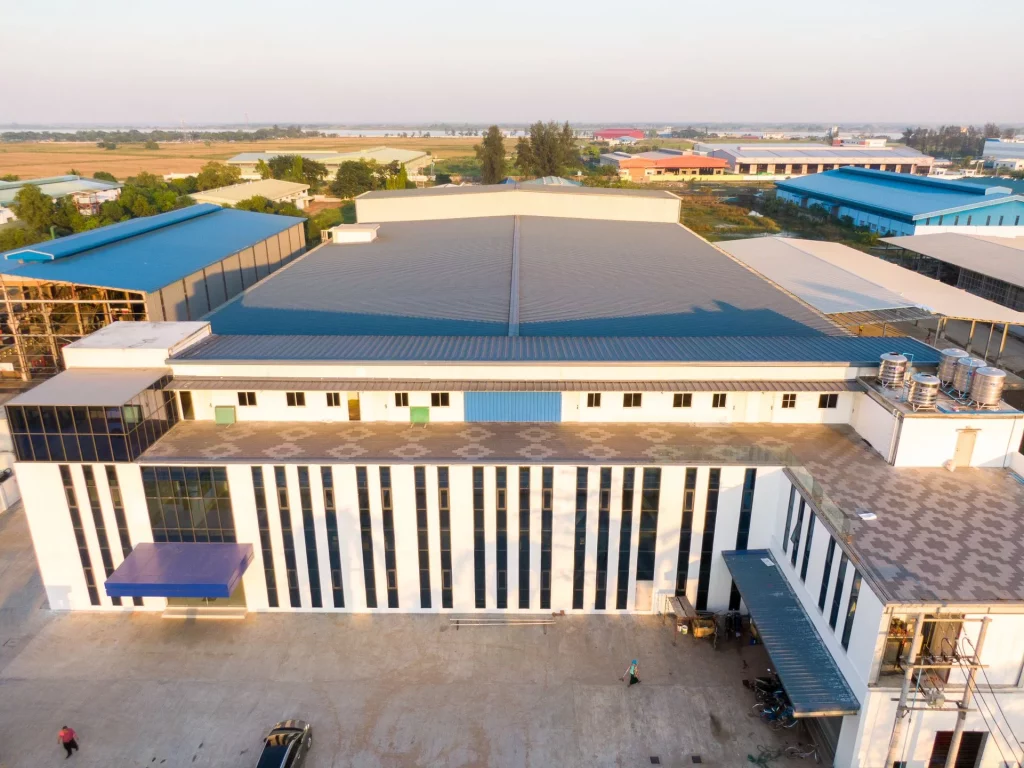
3.2. Construction Phase
Foundation Construction and Anchor Bolt Installation
- The first step in constructing an industrial factory is installing the anchor bolts, which is crucial as it lays the foundation for the entire structure.
- Any mistake in this step can significantly affect the components of the building, such as beams and columns.
- The foundation construction process should involve:
- Selecting a suitable foundation type: Choose a foundation type appropriate for the soil, load of the factory, and local geological conditions. Common foundation types include: isolated, strip, pile, and raft foundations.
- Excavating the foundation: Use machinery or manual labor to excavate the foundation according to the designed dimensions and depth.
- Installing the foundation pile system (if necessary): For pile foundations, pile driving or pressing should be done following the technical procedure.
- Anchor bolts must be securely welded to the foundation reinforcement system. Welding should occur after the foundation formwork and reinforcement installation is completed to ensure the stability of the formwork system. The bolt heads should be carefully capped to prevent rust or contamination.
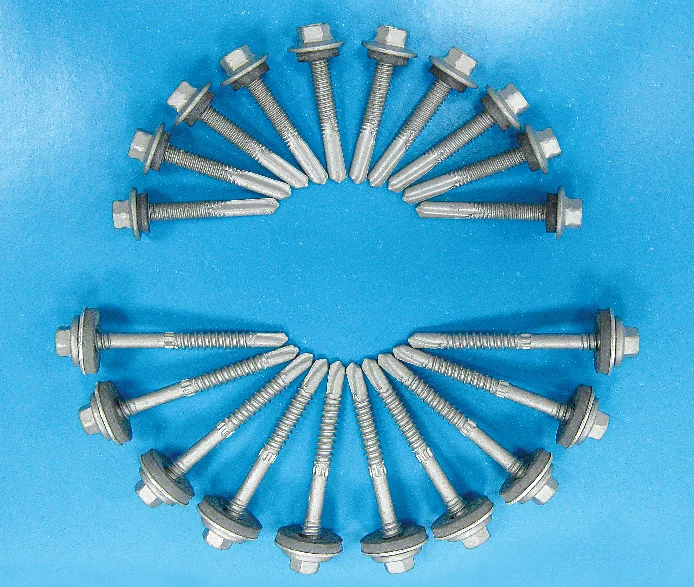
Material and Structural Component Transportation
- After processing and quality-checking the materials and steel components at the factory, they will be transported to the construction site.
- Once all materials are assembled at the erection site, the construction team will begin assembling the steel frame according to the technical drawings.
Column, Truss, and Purlin Installation
In this stage, due to the heavy weight of steel components, machinery is required for lifting and transporting during installation. The steps include:
- Installing the rigid frame
- Erecting the truss
- Completing the frame
- Installing the truss and purlins
- Erecting the gable truss
- Erecting purlins and purlin braces
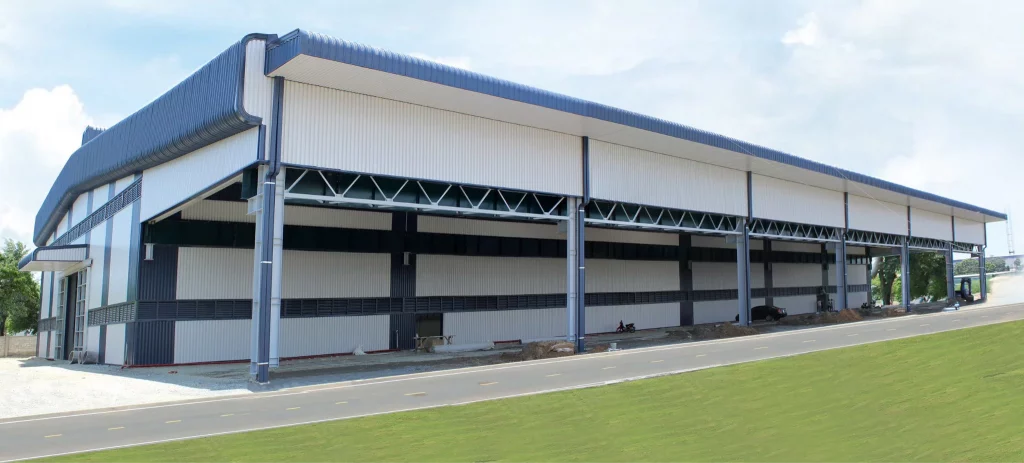
Precast Concrete Slab and Wall Installation
- Installing the concrete slabs and precast walls must follow the technical design plan.
- Based on the fixed anchor bolt positions, the concrete slabs are lifted and installed precisely.
- After ensuring the alignment with the upper purlin/tie beam through bolt connections, workers will tighten the bolts on both the top and bottom to secure the position.
Roofing Installation
- Selecting roofing materials: Choose materials suitable for the climate, usage requirements, and financial capacity. Common roofing materials include: galvanized sheet metal, insulated sheets, fibro cement sheets, etc.
- Installing the roofing support system: Install the roofing support system according to the design, ensuring it is sturdy and capable of bearing the load.
- Roofing: Install the selected roofing material according to the technical procedure, ensuring waterproofing and safety.
- Installing the drainage system: Install a roof drainage system to collect and channel rainwater out.
- Roof installation involves placing each sheet on a sliding tube, securing it with hooks, and pulling the tube to lift the sheet onto the roof. The construction workers will attach the sheets to the roof purlins, continuing this process until the roof is completed.
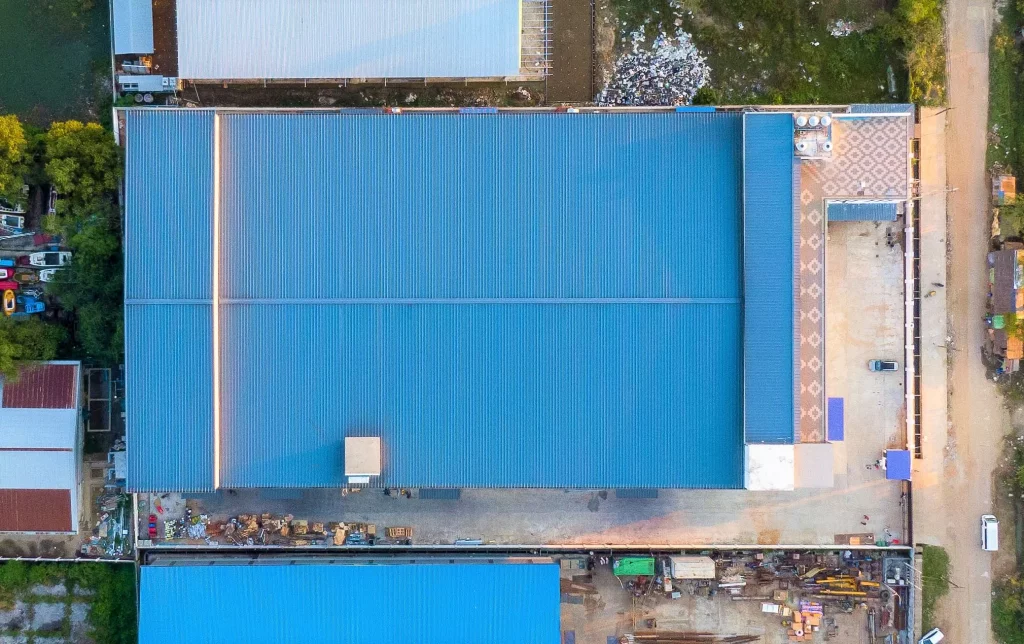
Infrastructure and Technical System Installation
- Factory infrastructure includes elements such as transportation networks, drainage systems, ventilation, gutters, and wall materials.
- Electrical system installation: Install underground or exposed electrical systems according to design, including electric cables, sockets, switches, distribution boards, fire alarms, etc.
- Water system installation: Install water supply and drainage systems.
- Additional infrastructure amenities, such as gypsum ceilings and green gardens, can also be built to enhance the aesthetic appeal of the building.
3.3. Post-Construction Phase
Acceptance and Handover of the Project
- Once all construction steps are completed, the contractor should inspect the quality of the columns, trusses, bolts, and roof connections, as well as seal any gaps at the ventilation openings, and then clean the entire factory. If everything meets the requirements, the contractor will proceed with the acceptance and handover of the factory to the client.
Cleaning and Handover of the Project
- Thoroughly clean the entire factory construction area, removing waste, dust, and excess materials.
- Re-check the construction quality, ensuring all items meet technical requirements.
- Handover the project to the investor following the agreed acceptance report.
Regular Maintenance
- Create a regular maintenance plan for the factory according to the manufacturer’s guidelines.
- Regularly inspect items such as the roof, electrical and water systems, doors, etc.
- Clean and maintain ventilation systems, drainage systems, and other equipment in the factory.
- Promptly repair any damages to ensure safety and efficiency.
Factory Upgrades
- Upgrade the factory as needed to meet new production demands or technological changes.
- Expand the factory area if necessary to increase production capacity.
- Install additional equipment and automation systems to improve production efficiency.
- Improve the lighting and ventilation systems to ensure a good working environment for employees.
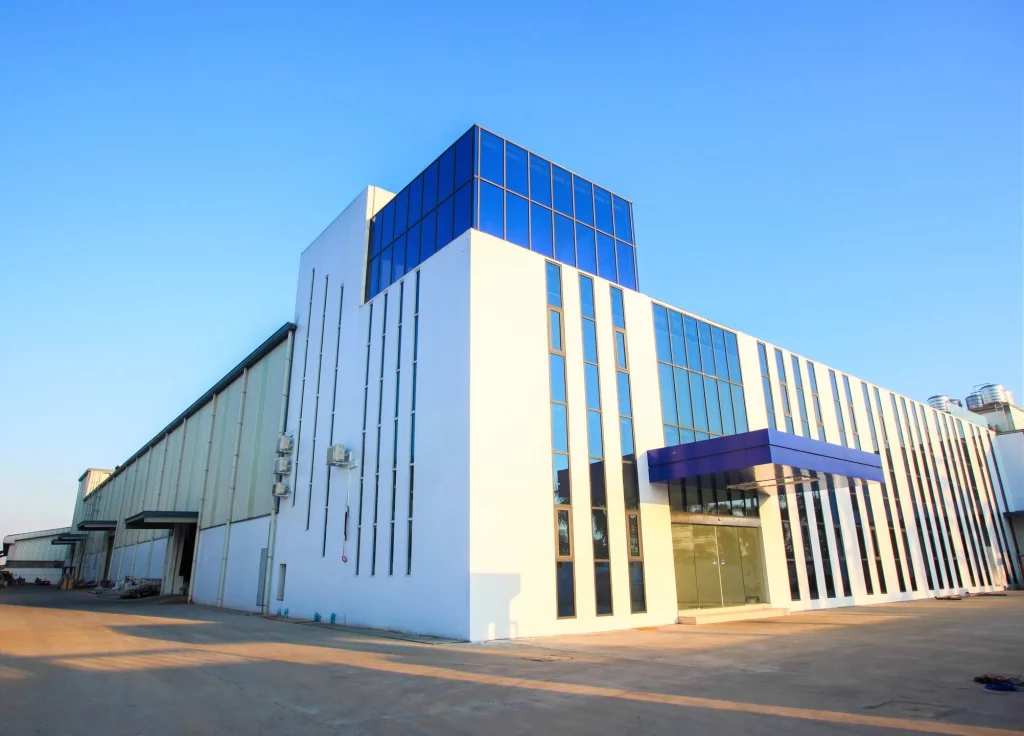
4. Some Considerations in the Industrial Factory Construction Process
4.1. Planning and Design
- Site Selection and Preparation: Ensure that the land is reasonably planned, with convenient transportation and the ability to support the building’s weight.
- Detailed Technical Plan: Structural calculations, foundation design, material specifications, and construction methods must be clearly defined.
- Compliance with Regulations: Must meet building codes, safety standards, environmental regulations, and accessibility requirements.
4.2. Construction Phase
- Foundation Structure: The most crucial part of factory construction is the foundation structure, so the contractor should focus on this stage.
- Steel Column and Truss Length Calculation: Carefully calculate the length of steel columns and trusses to avoid excess or shortage.
- Frame Stability: To ensure frame stability, brace installation should be done securely.
- Sequential Installation: During construction, prioritize installing rigid braces first, followed by other elements such as columns, trusses, purlins, and roof braces.
- Precast Concrete Panel Selection: Choose the appropriate size (height, thickness) and function of the precast concrete panels based on usage needs.
- Roof Sheet Installation: Follow the standards for roof sheet installation, ensuring that connections are aligned and perpendicular to the purlins to maintain quality and aesthetics.
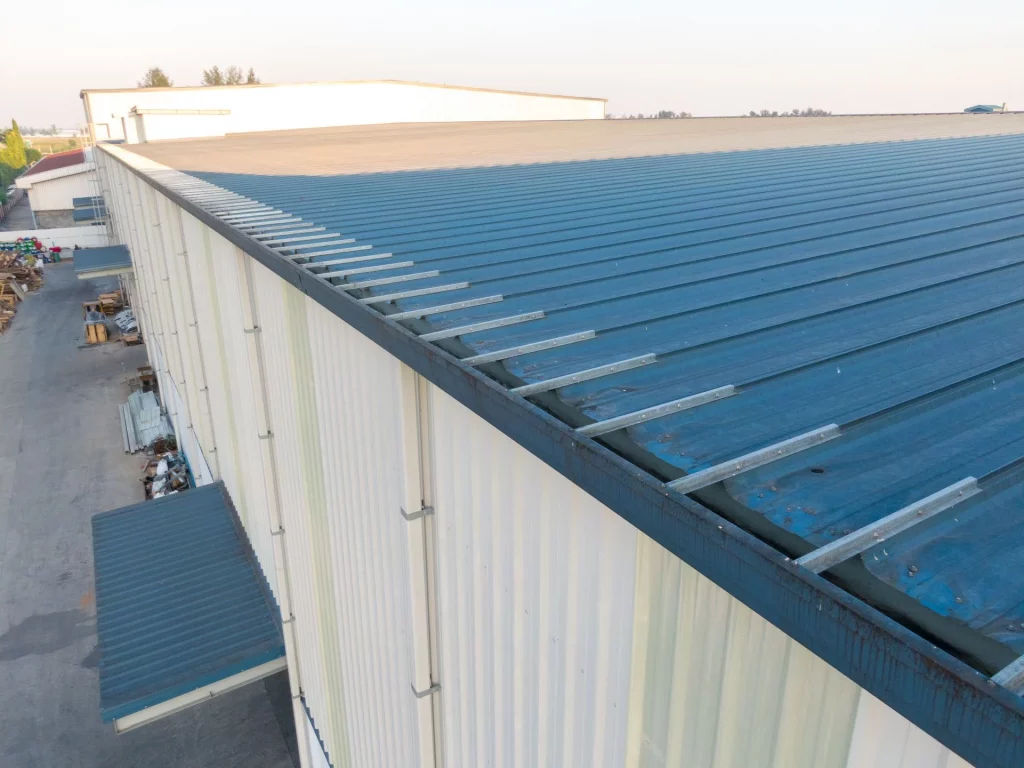
4.3. Utilities and Systems
- Electrical System: Safe and efficient installation of wiring, transformers, and distribution panels is necessary.
- Water Piping System: Address clean water supply, sanitary waste disposal, and potential treatment water needs.
- HVAC System: Properly sized heating, ventilation, and air conditioning systems to provide comfort for users and meet processing needs.
- Fire Protection System: Suitable sprinklers, fire alarms, and fire-resistant materials are essential for safety.
4.4. Safety
- Workplace Safety: Proper use of personal protective equipment (PPE), fall prevention measures, and adherence to safety procedures are paramount.
- Emergency Preparedness: Fire drills, evacuation plans, and appropriate hazard signage are necessary.