Many companies and individuals are increasingly opting for prefabricated steel warehouses due to their significant advantages in cost-efficiency and construction speed. The process of designing and constructing a warehouse typically involves several essential steps. Understanding these steps and key considerations is crucial for anyone interested in warehouse construction. Explore Pebsteel’s detailed guide below for insights into building a warehouse efficiently.
1. Warehouse Construction and Design Process
Pebsteel’s warehouse construction and design process is carried out precisely as follows:
1.1. Generate ideas & Propose solutions
First, Pebsteel will rely on information about scale, usage,… provided by customers to come up with ideas and offer different solutions for warehouse design. At the same time, the company also evaluates and advises on the most optimal choice for customers.
1.2. Contracting
After agreeing on the construction plan and quote, Pebsteel and the investor will agree on the necessary terms and then sign the contract.
1.3. Develop warehouse design technical drawings
With the agreed construction plan, Pebsteel will make detailed drawings of each item, specifically design, architecture, structure and construction materials.
1.4. Machining
When pre-fabricating steel structures, Pebsteel absolutely complies with the technical requirements on the drawings and regularly supervises the construction process. This is to ensure that the machining is carried out according to detailed techniques, avoiding errors.
1.5. Installation
After being pre-fabricated, the structural steel parts, pillars, etc. will be transported to the construction site and erected according to the drawings. Construction engineers will strictly monitor to ensure the most perfect quality.
1.6. Warranty
Pebsteel commits to a 3-year warranty on steel structure materials and 10 years on structures, and also always ensures a quick and accurate handover of the project as planned.
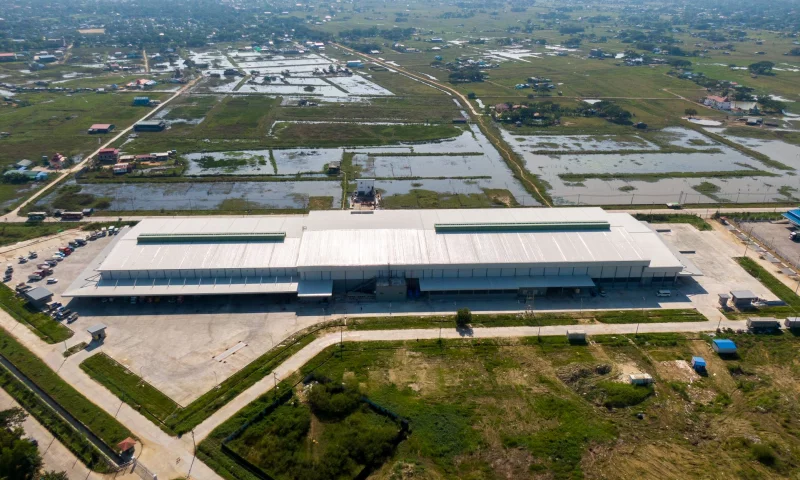
2. Advantages of Using Prefabricated Steel Building in Warehouses Construction
2.1. High durability and good bearing capacity:
High bearing capacity: The steel frame is made from tempered steel with good bearing capacity, vibration resistance, impact resistance, suitable for storing heavy, bulky goods.
Good fire resistance: Steel structures are coated with specialized fire-retardant paint, helping to limit the spread of fire and protect the safety of goods and property.
Anti-termites and insects: Steel frames are not affected by termites and insects, and have a longer lifespan than warehouses using traditional materials such as wood.
2.2. Flexibility in design and construction:
- Diverse Design: Prefabricated steel buildings can be designed in a wide range of styles and sizes, catering to diverse usage requirements and customer purposes.
- Easy Expansion: The warehouse can be easily expanded by adding new steel frames, the ability to easily expand the floor area of the warehouse by adding new steel frames, in line with the business’s growth needs.
- Simple Relocation: Steel structures can be easily disassembled and moved to another location without compromising the quality of the structure.
2.3. Diverse applications:
- Industrial Warehouse: Storage of raw materials, finished products, machinery, and equipment for manufacturing plants.
- Goods Warehouse: Storage of goods for commercial and service businesses.
- Factory: Suitable for light industries, food processing industries, textile industries, etc.
- Stadium, Arena: Used for sports and entertainment activities.
- Garage: Storage for cars, motorcycles, etc.
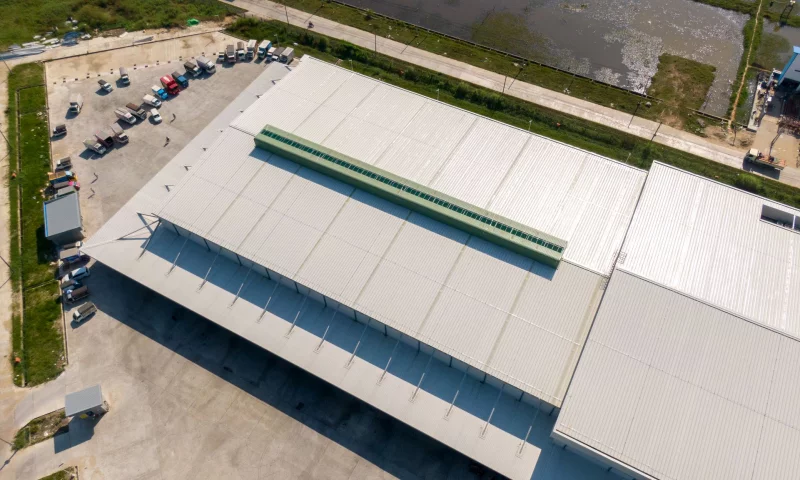
2.4. Sustainable commitment
In an age where sustainability is paramount, steel’s recyclability has emerged as a key feature, in line with global efforts towards sustainable construction practices and reduced carbon emissions of industrial buildings.
2.5. Cost effective
The cost of building a prefabricated steel structure warehouse will depend on a number of factors, including the size of the warehouse, the type of steel used, the complexity of the design, and the location of the warehouse. In general, prefabricated steel warehouses are more cost-effective than traditional warehouses due to quick and easy assembly, as well as durability and low maintenance costs.
- Faster design and construction process:
If your warehouse plans are submitted to a steel structure manufacturing company, the building will be pre-designed and manufactured by experts. It enhances the overall cost-effectiveness of the entire process, as pre-manufactured steel construction parts are directly shipped to the construction site.
- It has reduced labor costs:
Due to the prefabricated nature of warehouses, construction time can be significantly reduced by 30% to 50% or even more, depending on the expertise of the construction team. As time is valuable, faster construction leads to reduced labor costs.
- Reduce maintenance costs:
Due to low maintenance costs of steel structures, building owners save on general maintenance, repair and replacement costs throughout the life of the project.
2.6. Space
Steel structures are a cost-effective choice for large-scale warehousing, manufacturing, and distribution operations. They provide the industry’s widest clear spans, maximizing usable space and minimizing structural obstructions. This allows for the installation of large industrial machinery, vehicles, and personnel within the building. Furthermore, steel structures ensure the safe movement of personnel and equipment.
2.7. Environmental friendliness
Saving construction materials : Uses less construction materials than reinforced concrete houses, contributing to protecting natural resources.
Modern production process : Applying modern production technologies, limiting dust and noise emissions into the environment.
Recyclable : Steel structures can be recycled after the end of their useful life, contributing to reducing construction waste.
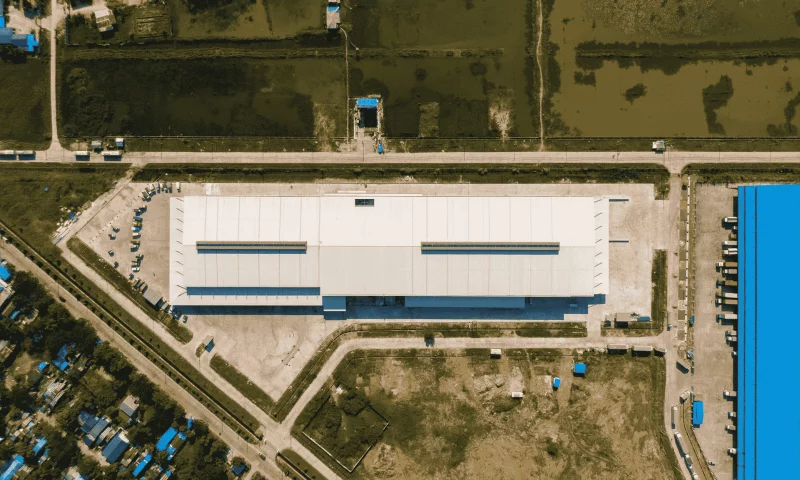
3. Pebsteel’s Pre-engineered Steel Warehouse Quotation Process
A prefabricated steel warehouse is a type of house built with pre-fabricated steel components and installed according to the engineer’s detailed drawings. Currently, the construction and construction of prefabricated steel buildings has gradually become a popular trend to replace the traditional method of using reinforced concrete.
Pebsteel is a leading design, construction and pre-engineered steel building company in the world. Possessing more than 27 years of operating experience in Asian countries and a team of highly specialized staff, Pebsteel is proud to meet the diverse needs of customers.
With the desire to provide quality prefabricated steel warehouse designs with reasonable costs, optimal for customers’ budgets, Pebsteel’s quotation process is always transparent and detailed.
- Consulting : The company’s team will find out in detail the customer’s needs, develop preliminary drawings, then propose solutions, accompanying materials and propose construction quotes for the design. prefabricated steel warehouse. After the customer approves the proposal, the company will confirm the final construction unit price to begin the construction process.
- After signing the contract : Pebsteel will create technical drawings to proceed with the production, processing and erection stages.
Through the clear prefabricated steel warehouse design quotation process as above, Pebsteel will provide you with a detailed price quote appropriate to each project scale.
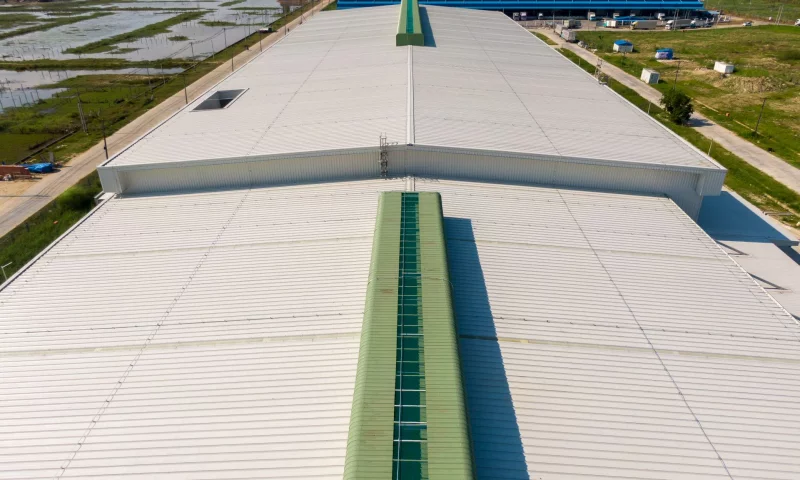
4. Means and Important Elements for Building Prefabricated Steel Warehouses
Building a prefabricated steel warehouse also requires attention to the same important facilities and factors as a conventional warehouse, however there are some differences due to the characteristics of prefabricated steel structures as follows:
4.1. Construction equipment
- Machinery and equipment : In addition to normal machines, specialized machinery for steel construction is needed such as: steel cutting machines, welding machines, punching machines,…
- Construction tools : Need additional specialized tools for steel construction such as: torque wrench, dead pliers, steel nailing hammer,…
4.2. Crucial factor
- Construction site : It is necessary to ensure hardness, flatness, and good load-bearing capacity due to the relatively heavy prefabricated steel structure.
- Design drawings : Design drawings need to be more detailed, clearly showing connection details between steel parts.
- Construction materials : Steel quality must meet standards, welds must be ultrasonic tested to ensure durability.
- Construction manpower : A team of construction workers with expertise in steel structures is needed.
- Labor safety : Special attention should be paid to labor safety when constructing steel such as: using safety belts, helmets, goggles,…
In addition, the following factors should also be noted:
- Anti-rust treatment for steel structures.
- Install lightning protection system.
- Periodic maintenance of prefabricated steel warehouses.
- By paying attention to the above means and important factors, you can build a prefabricated steel warehouse safely, effectively and cost-effectively.
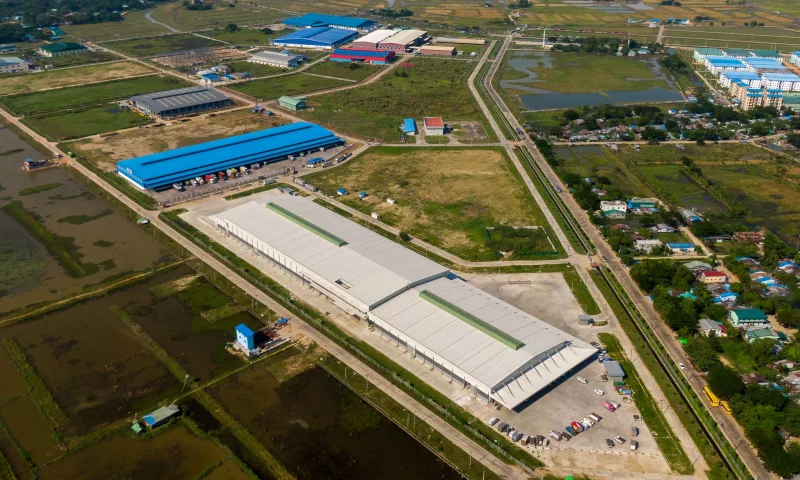
5. Key Factors Influencing the Unit Price of Prefabricated Steel Warehouse Construction
5.1. Type of material used
The quality of steel materials, corrugated iron, roof panels, windows, and doors directly affects the warehouse price.
Materials with clear origins and reputable brands often have higher prices.
5.2. Warehouse design and function
A complex warehouse design with many intricate details will consume more materials and labor, leading to higher costs.
Warehouses that require special functions such as insulation, fire protection, modern electricity, water, and ventilation systems will also increase costs.
5.3. Scale of warehouse construction
This is an important factor, greatly affecting the cost of construction and design of pre-engineered steel warehouses. With the same structural model and type of construction materials, the cost to construct a warehouse with a scale of 1,000 m2, 2,000 m2, 10,000 m2,… will be much different.
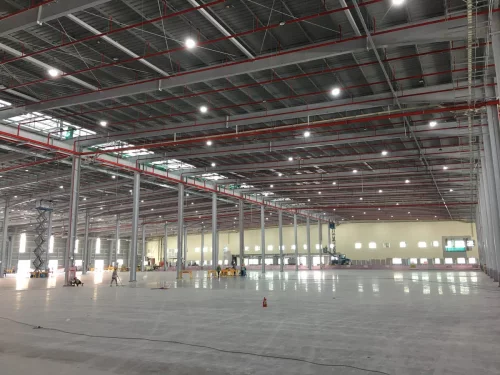
5.4. Warehouse model
Besides the construction location and total construction area, another factor that also greatly affects the warehouse construction unit price is the design.
Depending on whether the warehouse has a simple design or many complex details, one floor or many floors, whether it includes many sub-structural items or not,… which leads to many different prices for investors and developers. Bidders consider.
Warehouse design directly determines the load-bearing structural frame, type of material, and aesthetic solution. Therefore, customers need to find reputable consulting and construction units to have the best design.
5.5. Warehouse location
Location is an important factor that has a significant impact on the unit price of prefabricated warehouse construction. If the project is located in a land with good geology, it will save costs on the foundation.
Besides geological factors, environmental conditions surrounding the project also greatly affect construction costs because it determines what types of materials need to be used.
For example, a manufacturing plant in an area near the sea (which is highly corrosive due to the salty air) requires the investor to use special materials and modern material processing technologies to ensure ensure good corrosion resistance, so construction costs will be higher than a factory located in a plain area with a temperate climate.
5.6. Construction technical requirements
Complicated construction techniques, requiring high skills and modern equipment will also increase construction costs.
Warehouses have high safety requirements and need to install lightning protection systems, surveillance cameras, and fire alarm systems, which also lead to higher costs.
When designing a prefabricated warehouse, depending on the scale of the project as well as other objective factors, construction costs will vary. Below are some criteria that affect the unit price of warehouse construction.
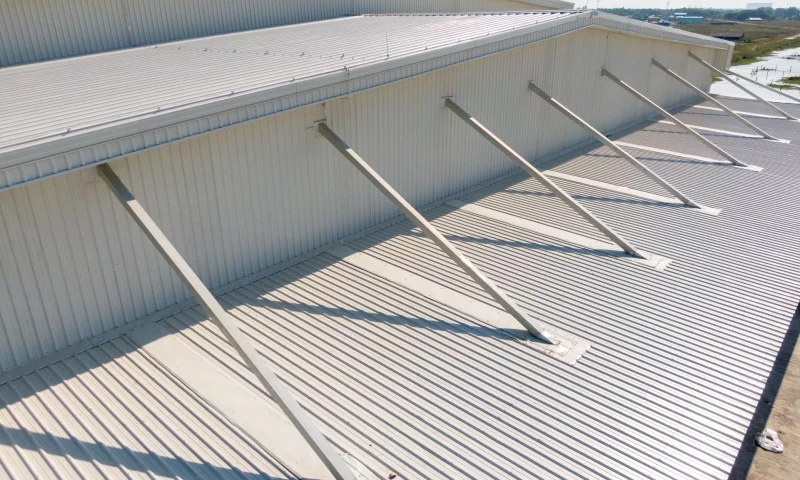
5.7. Construction time
Depending on the time of year the warehouse is constructed or the market situation, the unit price of materials (steel) will fluctuate differently. Therefore, the issue of construction time also affects construction costs. During the global COVID-19 outbreak, steel prices have spiked due to impacts on international production and transportation. Construction projects during this period were either delayed until construction was allowed and steel prices stabilized, or they had to incur huge material costs.
5.8. Warehouse construction progress
Warehouse design and construction time usually lasts 3 months from design to processing and erection. Some projects have longer construction times depending on the scale and complexity. Besides, if customers want to shorten construction time, construction costs will also increase.
5.9. Construction contractor
Currently, the market has many different prefabricated steel warehouse construction companies with different capacities, processes and quotation methods leading to different costs.
To get an accurate quote for a prefabricated steel warehouse, contact Pebsteel website for free consultation and survey.
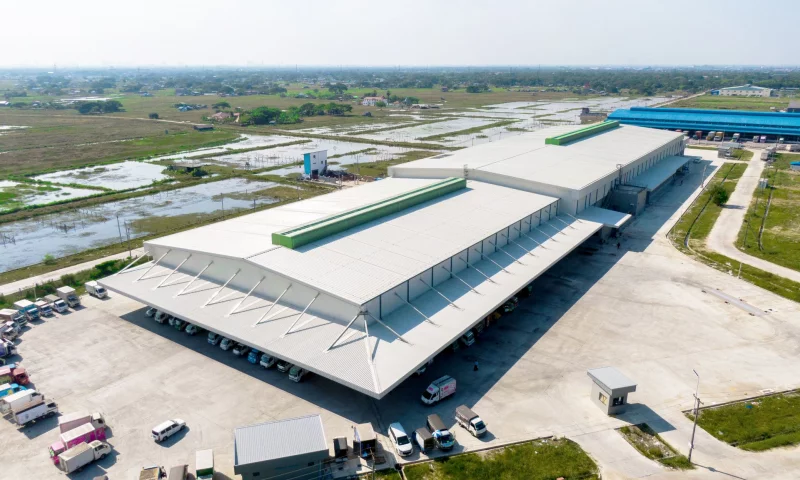
6. Construction Stages of Steel Warehouse Construction
The process of building a prefabricated steel warehouse includes many detailed work items and requires high expertise. Below is detailed information about each item in this phase:
6.1. Construction of the foundation
- Prepare surface:
Clean and level the construction site, ensuring it is flat and clean.
Determine the center and edge of the foundation according to the design drawing.
Dig the foundation hole according to the size and depth shown in the drawing.
Treat the foundation if necessary such as: replacing soft soil, lowering underground water level,…
- Construction of piles and foundation stations:
Pile driving: use reinforced concrete piles, steel piles,… suitable for the project’s geology.
Construction of the foundation: pour concrete into the foundation, connect the foundation with the pile with anchor bolts.
Installing the foundation beam system: linking the foundation stations together with reinforced concrete beams, ensuring even load distribution on the foundation.
- Quality inspection of the foundation:
Check the concrete strength, settlement and tilt of the foundation.
Check welds and anchor bolts to ensure safety.
There is a record of acceptance of the foundation before proceeding with the construction of the frame.
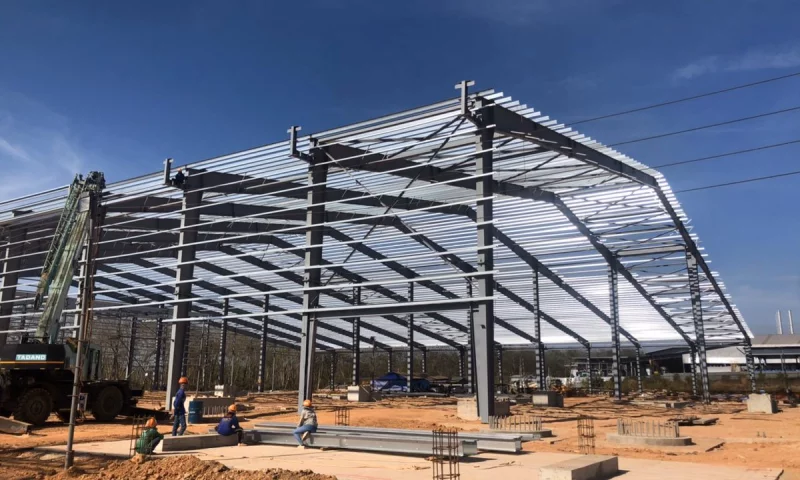
6.2. Installing steel house frames
- Prepare:
Check and ensure the quality of steel structures before erection.
Prepare cranes and necessary auxiliary equipment for erection work.
Locate columns, beams, and trusses according to design drawings.
- Column erection:
The crane erects the steel column into the predetermined position, using anchor bolts to connect the column to the foundation.
Calibrate and adjust column position accurately according to axis and elevation.
Weld and secure the column to the foundation.
- Beam erection:
Crane the steel beam into position and place it on the erected columns.
Install connection bolts between beams and columns.
Weld the beam to the column.
- Installing trusses:
Crane the steel truss into position, placing it on the installed beams.
Install connection bolts between trusses and beams.
Welding and fixing the truss to the beam.
- Installing bracing and anti-buckling:
Install diagonal bracing and wind bracing to ensure stability for the steel frame. Install bucking bars to limit horizontal movement of the house frame.
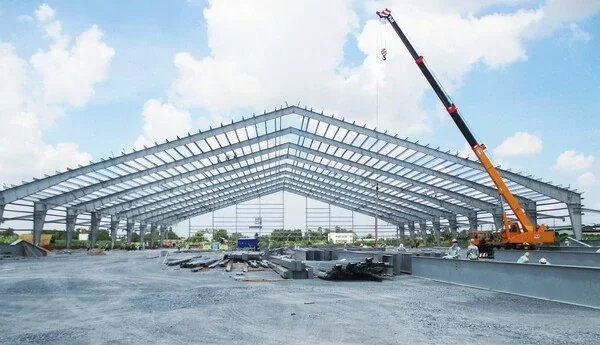